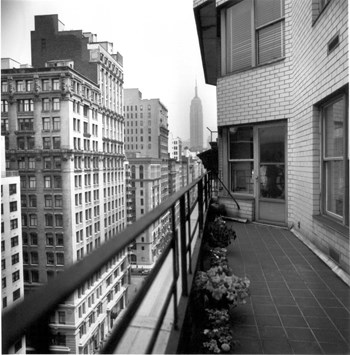
Whether you are looking out over New York City from New Jersey or looking out from New York City towards New Jersey or Long Island, the skyline is lined with high-rise cooperatives and condominiums—the majority of which are now close to 30 years old. Subject to the harsh environmental conditions common along the coast, age, natural wear-and-tear and lack of maintenance, co-op and condo boards are now faced with upgrading and repairing their plaza decks.
A thorough understanding of the issues and challenges that can arise during a plaza deck restoration project, as well as the basic steps in the repair process, will help ensure that the project is bid correctly from the onset and monitored properly throughout the process.
Bidding the Project
Plaza deck restoration projects are usually awarded based on a competitive bid process. The co-op board or condo association hires an engineering firm that performs a detailed survey of the plaza deck, quantifies the deterioration, analyzes the structural integrity of the base structure, provides a set of plans and specifications for competitive bid, chooses the bidders, holds a pre-bid conference and analyzes the bids.
The board usually then opts to bring in the three lowest bidders to see if they understand the project and determine if there are any further reductions in price. It is at this point where a plaza deck restoration project will choose its fate as to whether it will be successful or end up in the legal system with a bunch of unhappy shareholders or unit owners, who just spent a huge amount of money for a leaky, problem-riddled, "new" plaza deck.
Unfortunately, most co-op or condo boards choose the contractor based on a financial decision. After all, the contractors that bid are all called "restoration contractors" and selected by the engineer. But are all restoration contractors equal? Do all restoration contractors share the same culture in safety, quality, management and financial stability? Is the restoration contractor a small company where the principal does the sales, estimating, project management, billing, etc.? Will the contractor be around during the warranty period if a problem should arise? Does the contractor have enough resources (manpower, equipment, knowledge) to handle any unforeseen conditions or delay?
A typical plaza deck restoration project consists of the following major work items: demolition of existing topping, planters, amenities, landscaping, waterproof membrane, as well as mechanical, electrical and plumbing systems. After the demolition is complete, a typical project then consists of repair to the structural base elements, replacement of a waterproof membrane followed by new concrete surfaces, planters, landscaping and deck amenities.
Because the footprint of the deck cannot grow or shrink, nearly all the work items in a typical unit price plaza deck contract are a fixed cost for the owner. The unit price concrete repair line items can increase or decrease the overall budget for the project based on how much deterioration is found during the project. It is almost impossible to determine with any degree of certainty the amount of structural deterioration that lies below the topping slab or existing membrane. Only upon removal of these areas can the extent of deterioration be determined. It is not prudent for an owner to bid the unit cost repair work as a lump sum and put the risk onto the contractor.
Demolition of the Plaza Deck
Because of the potential for damage to the property, public and contractor's personnel, by far the riskiest step in the repair and restoration process is the demolition process. Proper planning and phasing are critical to success.
Since contractors are working in active structures, proper care must be taken to protect all surrounding surfaces and public access points. A contractor that can provide a health and safety demolition plan prior to the start of the work on a proactive basis is a contractor of choice; whereas, a contractor that doesn't plan merely reacts to the hazards after they occur. A pre-job condition survey should be performed and documented both by video and photo to document all pre-existing conditions to a property.
A health and safety demolition plan should be both written and drawn. The plan should identify areas that need protection, phased walkways, modified traffic patterns, signage, utilities that need to be protected or rerouted, personal protective equipment, ventilation plan, public protection, vehicle protection, phasing around pool usage periods, dumpster location, shoring plans, equipment location, demolition procedure, load out procedure, hazard recognition, site specific safety respiratory and hazardous communication plans, emergency action plan, emergency contact list, call before you dig, building intake protection, etc. Many problems can be prevented before the incident occurs with a proper demolition pre-plan. This plan will also assist in the event of an OSHA site inspection where the site could potentially get shut down due to the lack of a plan.
Embedded conduit within the demolition area should be pre-determined and budgeted properly. Too often, owners incur unanticipated additional costs due to damage of embedded conduits that are not identified prior to demolition. A contractor cannot anticipate the location of the embedded items; therefore, a unit price contingency should be put into the bid documents.
In conjunction with proper planning, effective and experienced project management is an important part of the process to keep risks in check. Proper shoring and demolition equipment selection are essential so as not to overload the structural slab or create a life safety hazard to the demolition crew. Stock piling debris on a structural slab is also a procedure that should be kept to a minimum.
Open holes, fall protection, proper scaffold training, temporary barricades, signage, temporary protection from the weather, housekeeping, near-hit reporting, safety attitude and behavior, etc. are just some of the qualities an owner should consider in a restoration contractor. All too often, owner's are focused on the bottom-line bid from a contractor without realizing the "down the road" financial impact that an owner may be subjected to if an incident occurs from either property damage or more important, bodily injury.
Restoration contractors with a strong safety culture should be used by the owner in their selection process. Personal protective equipment should be worn at all times by the contractor's employees as well as the subcontractors. A restoration contractor with the ability to manage safety not only for their own employees, but also the subcontractor's employees will reduce the risk of possible liability.
Surface Preparation and Waterproofing
Most failures in plaza deck restoration occur because of poor surface preparation for the new waterproof membrane application. Failures range from too much preparation to not enough preparation.
Surface preparation methods can include sandblasting, shotblasting and high-pressure water blasting. Removal of existing membranes or coatings needs to be achieved in order for the new membrane to bond properly to the substrate. The desired profile of the substrate is dependent on the material used to waterproof the deck. Different materials require different profiles, so an overly aggressive surface preparation method that either exposes aggregate or creates high amplitude in the profile may impact the waterproofing integrity of the product.
Another pitfall of surface preparation is lack of understanding about the moisture content as well as the moisture transmission in the substrate. Too much moisture or moisture transmission will compromise the new membrane by causing failures along the bond line or creating pin holes in the new membrane from out-gasing. Failures occur from placing the membrane on newly placed concrete without achieving proper cure, installing the membrane directly after a rain storm or power washing of the surface or even placing the membrane during the wrong time of day.
There are several tests a qualified restoration contractor can perform to ensure proper moisture content and transmission prior to installing the membrane. Further, there are also tests to ensure bonding. These tests are not always outlined in the specification. A prudent contractor has the knowledge to perform these tests prior to the installation of the new membrane.
Obviously, a qualified licensed applicator is required to install these membranes. Specifications may require that a contractor have a number of years using certain products and submit a copy of their licensing agreement with the manufacturer. Proper flashings, terminations, product mixing, heating, etc. are all details that require intense attention. Since the manufacturers are tied into the warranty with the applicator, manufacturers should provide written feedback and be involved in approving the surface preparation and proper installation of the waterproofing system. Water testing the membrane prior to installing any topping is the proper procedure to employ when all waterproofing activities are completed.
The waterproof membrane, in essence, is the determining factor in whether a plaza deck restoration project will be successful. After all, what is the sense of have a new plaza deck that leaks? What will the shareholders think of the condo board that selects a restoration contractor that doesn't pay attention to the details in order to save a few bucks?
A Concrete Solution
Any contractor can place concrete, but can any contractor place concrete the proper way? Is there a proper way to place concrete? Obviously, there is a proper way to place concrete and not every contractor knows the proper procedure.
Whether your new plaza deck calls for stamped concrete, colored concrete or standard concrete, the concrete must be placed in the proper manner. The American Concrete Institute (ACI) has a set of guidelines that should be followed for any concrete placement operation.
Pitfalls with new concrete stem mostly from installation errors. Examples include too much water, not enough air entrainment, too much entrapped air, poor curing methods, improper placement of reinforcing steel, re-tempering the concrete mix, over-finishing, improper vibration (consolidation), use of chloride accelerators, improperly placed control joints, etc. All of these factors are controllable and mostly affect the porosity and the strength of the concrete, which ultimately affects the durability of the concrete. Concrete durability is particularly important in a climate of freeze-thaw, like that found in the New York City metro area.
Cracking is another area where owner's expectations are sometimes not met. Non-uniform geometric shapes in flat work will induce shrinkage cracking. Sharp corners from building edges, drain bodies, pool corners, etc. all facilitate cracking. This type of cracking is not a result of installer error, but poor design and location of control joints. Owners need to understand concrete cracks. Control joints are placed in the concrete to help control cracking, but not all cracking can be captured by control joints; therefore, there is acceptable cracking in concrete. Obviously, some cracking can be the result of installer error. The contractor and engineer should work together to determine a concrete control joint plan prior to placing concrete.
Aside from finish concrete, structural concrete repairs require even more attention to detail. After all, the structural shell of the plaza is the support of the plaza. The International Concrete Repair Institute (ICRI) provides a set of repair standards that have been incorporated into the ACI standards. Simple partial depth spall repair has a multitude of important details that must be followed in order to ensure a long lasting repair as well as a true structural fix. Details such as chipping under existing reinforcing steel, saw cuts along the repair perimeter, proper repair geometry, proper concrete removal equipment and methods, shoring, surface preparation of substrate, cleaning corroded reinforcing steel, proper choice of repair material, proper installation and curing procedures are a few of the critical details of a simple spall repair. Because of the age and degree of deterioration a structure may have endured, there may be many structural elements that may need to be repaired—each with specific required details for the proper repair. Shortcutting one detail may result in a failed repair and loss of structural integrity of the structural shell.
All About Planters
Plaza deck planters come in all sizes and shapes with multitudes of different construction including landscape block, concrete, wood and masonry to name a few.
Most problems with plaza planters have to do with drainage. Some designers opt to build the planters on the new topping slabs. In construction such as this, drainage from the planter to the new topping slab leads to unsightly staining on the new concrete topping slab.
Some designers put a great deal of engineering into the pitch of the new topping slabs only to find when the new planters are installed that the new planter placement restricts flow to the slab drains and unsightly puddles form.
Selecting the proper material for construction of the deck planters is essential. Waterproofing landscape block that conforms to irregular shapes is quite challenging. The use of drainage matting and protection around drains inside the planter are often done improperly, which leads to problems.
Annual maintenance performed by the owner in and around planter drains must be planned for and done periodically. If a planter drain clogs, the planter will relieve itself onto the finished surface causing staining and unhappy shareholders.
Installing the Expansion Joints
Aside from the normal waterproofing details and tie-ins, improperly installed expansion joints are a leak source.
Choosing the correct expansion joint for the type of structure and use is extremely important. Tying the waterproof membrane into the expansion joint system is equally as important.
Expansion joints need to be sized or fitted to the deck. Movement range can be calculated for an expansion joint on almost any structure. Installing the expansion joint blockout to the correct size for a particular installation temperature is essential for the proper installation of the gland.
Expansion joint mitres, upturns and terminations are all potential leak sources and should be detailed. The experience of the contractor's technicians will dictate the completeness and water tightness of the expansion joints
Punch List and Completion
The last 10 percent or completion of a project usually seems to take the longest to finalize. At substantial completion, an owner's representative should prepare a final punch list. A final punch list should be just that—final. More often then not, punch lists turn into a never-ending "to do-list." New items keep getting added to the list on a weekly basis, which extends into the warranty period and before long, warranty items are then added to the punch list. The owner gets frustrated that the punch list is not getting done, the owner's representative is continually accruing hours and the contractor is not getting his final payment. The contractor then has to lien the project property and fights it out in litigation. This all can be avoided if a final punch list is established at completion.
Understanding the basic steps of a plaza deck restoration project is important to ensuring that the project remains on schedule. This knowledge will allow you to monitor the project's progress to ensure successful completion of a project this is both on time and within budget.
Bob Pirro is branch manager for the New York/New Jersey office of Structural Preservation Systems.
Leave a Comment