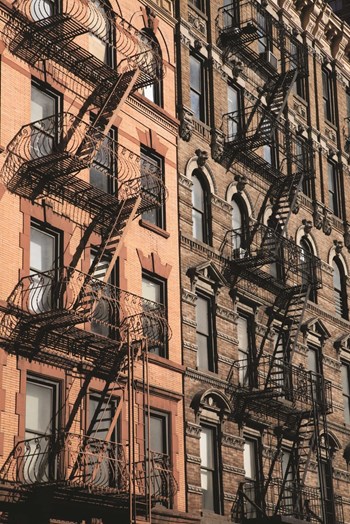
Walking down the streets of New York City, the zig-zag iron work of fire escapes immediately evoke romantic images of a simpler time, having been immortalized in books, songs and plays from West Side Story to Rent. With some fire escapes being as large as whole rooms, (measuring 31 ½ feet wide by 10 ½ feet long, and wrapped by a 2 ½ foot high railing in some neighborhoods), tenants have converted their fire escapes into personal spaces for years; from private libraries, meditation spaces, laundromats and arboretums to the ultimate skybox seat at New York Yankees games. As “classic New York” as this may be, one must not forget their real purpose.
Stephen Varone, AIA, president of RAND Engineering & Architecture, P.C. in New York City notes that, “A fire escape is a critical part of a building's emergency plans. You hope you never have to use it, but if you do, it needs to be ready and reliable.”
The fire escape has been a New York City icon since the mid-19th-century. Their inclusion in city laws can be traced back to Article 7 of the New York Consolidation Act of 1891 which states, “Every such house shall be provided with a proper fire-escape, or means of escape in case of fire, to be approved by the inspector of buildings.” But it wasn’t until the late 1920s, after a series of deadly fires, that the city began to enforce tough rules requiring that all buildings be outfitted with a fire escape or a second, enclosed stairwell.
Local Law 11
Local Law 11 began life in 1980 as Local Law 10, which required five-year inspections of the street-facing façades of buildings seven stories or higher. Local Law 11 of 1998 is a slightly updated version that now mandates the inspection of all façades, whether or not they are facing the street. Local Law 11 also requires scaffolding with each inspection, a report on the cause of any deterioration, and a timetable for repair. Upon inspection buildings are classified as "Safe," "Unsafe," or "Safe with a Repair and Maintenance Program" (SWARMP).
“Every five years, an engineer or architect performing the Local Law 11 facade inspection on your building should look for any unsafe conditions on the fire escapes,” says Peter Varsalona, P.E., who is principal with RAND. “Considered unsafe,” he says, “are any items or debris on the fire escape, such as flower pots, blocks or bricks (often used to secure window air conditioners), personal items, or anything that could fall from the fire escape or obstruct egress.”
Varsalona suggests first having your building's engineer look at the fire escape to assess its structural soundness. “The engineer should note all bent, loose, or missing parts, such as steps (also called treads), railings, slats, bolts, the supporting steel beams or angles that attach into the face of the building, cracked or missing caulking or bricks around the penetrations, rust, flaking paint, and any sharp edges or pieces of metal. He should also check the condition of the drop ladder that hooks on the second-floor landing of the fire escape and is lowered to the ground so people can climb down safely.”
Overall maintenance of your fire escape is relatively inexpensive as most of the work can be done by your established maintenance team. According to Larry Kaufman, fourth-generation head of the family-owned J. Kaufman Iron Works, founded in 1907, “ninety percent of the metal work in New York is steel or wrought iron.” This includes your fire escapes.
The bad news is steel and wrought iron are prone to rusting and therefore require constant vigilance by the building’s maintenance crew. “As soon as the rust starts,” warns Kaufman, “it’s like a cancer. When you see something that’s really old and has been neglected and is rusted, it almost peels away in your hands. Once it starts doing that, you’re done. The cost to fix it gets way up there.”
However the good news is that steel and wrought iron are relatively easy to maintain. These are two materials that on-site maintenance staff can care for without extensive training, and do not require a professional for maintenance.
Kaufman, whose company specializes in restoration, agrees. “I have buildings call us from time to time to do maintenance but I recommend they do it themselves.”
For Kaufman the trick is regular painting. “Whoever maintains your building, just let them take a wire brush and knock off anything loose and peeling and put on another coat of paint,” says Kaufman. “If continually painted, whether it’s on an annual basis, or semiannual, it will last forever.”
If there is long term neglect of fire escapes then, Cisco Meneses, owner and founder of Fire Escape Services, which provides services nationwide, says you should not be too complacent about merely scraping and painting them. “Is that what holds fire escapes together, paint?” he muses.
In his Fire Escape Academy, Meneses teaches inspectors and engineers from across the country to change their focus from “scrape and paint violations” to “repair and paint violations,” thus forcing owners and safety professionals to take a closer look at the entire structure. According to Meneses, new fire escapes have not been fully constructed on the whole since the 1930s. This means, he says, “we have fire escapes in this city which are bordering on 75 to 100 years old.”
According to Meneses, rust is definitely a major problem but structure is another. “One must look for structural cues that say whether or not this structure also needs refurbishment,” he says. More often than not it’s as simple as the bolts. “With every fire escape out there,” says Meneses, “if you want to know its age—look at the bolts. If it has a square head bolt or a rivet it’s 50 to 75 years or older. If it has a hex head bolt on it then it is 25 to 50 years. How easy is it now to see if the fire escape has original hardware on it or if it’s been refurbished? It’s just the bolt. It’s that simple.”
The lesson here: that if you have a fire escape with nothing but original hardware your building is definitely due for more than just a coat of paint. According to Varsalona, fire escape repairs beyond scraping, and painting, are relatively simple consisting of mainly tightening loose bolts and minor welding.
“The most critical elements are the steel beams or angles that penetrate the building wall and provide structural support for the fire escape. If they show signs of wear, they may need a supporting angle or reinforcing plate welded to them for added support.”
“If the steel is badly deteriorated,” Varsalona adds, “the beams will need to be removed and replaced with new ones, which requires removing the brickwork or masonry around the joints where they penetrate the wall. All joints around penetrations should be caulked to keep water out. Not only will water corrode the beams and loosen the fire escape's supporting members but it will also damage the brickwork and allow leaks to find their way into the building. Loose steps, railings, platform slats, handrails, and other metal pieces should likewise be bolted or welded as necessary.”
Time to Paint
When it comes time to paint make sure all rust is scraped off as well as any loose, blistering, peeling, or flaking paint. This can be the more time-consuming aspect but it must be done.
“If the fire escape has been painted over several times and the underlying paint wasn't properly removed,” says Varone, “then sections of it may have to be scraped down to the bare metal. The metal is typically cleaned with a power washer and dried, and then a rust-inhibitive primer and enamel-based paint are applied. To keep the fire escape in uniform condition, it's recommended that the whole assembly be painted at one time rather than just portions of it.”
Varone also recommends that before removing the paint on an older or historic structure the association board may need to hire an environmental firm to test the paint for lead and asbestos. “If either one of these materials are found, then you will be required by New York City law to undertake an extensive—and often expensive—lead and/or asbestos abatement project.
This would entail hiring a lead/asbestos abatement firm, which must follow strict OSHA rules, such as using a wet-based removal method instead of dry scraping (which produces air-borne particles) and sealing all windows to prevent hazardous dust or residue from entering apartments. If the paint doesn't contain lead or asbestos, the contractor can use standard paint stripping methods with the usual precautions.”
The board must also find out if the building is in a New York City-designated historic or landmarked district. If that is the case, Varone adds that the building will need to obtain a permit from the Landmarks Preservation Commission (LPC) for any repair or alternations. “The LPC will want to make certain that the fire escape is painted in a historically-accurate color.”
Retired FDNY Deputy Chief Vincent J Dunn has estimated there may be only 200,000 fire escapes left in New York City. It’s not quite certain how much longer the iconic fire escape will be with us. Post 9-11 climate and new construction are forcing them to be obsolete as they are replaced with fireproof internal stairs.
As much as they are part of our identity as New Yorkers—as residents, fire escapes are key to our survival in an emergency. You may never know if you’ll ever have to use your fire escape but keeping it well maintained is the best insurance you can have.
J.M. Wilson is a freelance writer and a frequent contributor to The Cooperator.
4 Comments
Leave a Comment