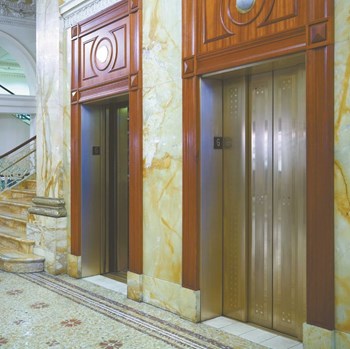
Ever since the first hydraulic passenger elevator was installed in New York City in 1870, the city has relied upon elevators to support its upward growth. Given that few would care to contemplate living or working in a 20-story walk-up, transporting people upward and back down again quickly and safely was a crucial component to the Big Apple’s development into a world-class city.
According to the U.S. Department of Labor Statistics and the Consumer Product Safety Commission (CPSC) however, escalator and elevator accidents claim about 30 lives and injure about 17,000 people annually in the United States.
Workers that maintain or clean the elevators account for almost half of the fatalities caused by elevators. The remaining half are casualties due to fall accidents in elevator shafts. There are also numerous cases of people being caught between moving parts of the elevator, collapsing platforms, stuck between doors, hit by counterweights, etc. Tragically, most of these incidents could be prevented through careful attention to safety and maintenance requirements.
Today, there are almost 60,000 elevators operating in the five boroughs. Of these, several are at work in co-op and condo buildings, some making hundreds of trips per day. Co-op boards and building owners—not elevator maintenance organizations—are ultimately responsible for the safety of a building’s elevators. Keeping these elevators safe and functional is one of building administrators’ most important duties, so it’s equally important that they stay on top of maintenance and inspection schedules, as well as promoting basic elevator safety among their residents.
Safety 101
So, is it possible for the average elevator-rider in a mid- or high-rise co-op or condo building to know at a glance if the lift they’re about to enter is safe? They can just take a look at the inspection certificate posted inside the cab, right?
Actually, no. While in a perfect world an up-to-date inspection certificate would be enough to assure a rider that their elevator is safe and fully functional, in real life, certificates are only as accurate as the people filling them out—and human error is sometimes unavoidable.
Only certified elevator inspectors can really determine whether an elevator is safe for passengers, and a total work-up on a given elevator goes well beyond the annual inspection required to renew the unit’s certificate. So even if a certificate seems to be up-to-date, that’s no guarantee that every inch of the cab and machinery has been professionally assessed.
Local laws govern elevator inspections and spell out what types of inspections must be done, and how often. The Department of Buildings (DOB), which oversees all construction and alteration of buildings in New York City, is required to perform routine inspections but the DOB inspection alone is insufficient to guarantee elevator safety. “The city inspection is purely visual,” says Hubert Hayes, president of the Brooklyn-based elevator consulting firm Hubert H. Hayes, Inc. “They don’t carry tools—they only inspect for maintenance, not for safety.”
Prior to being recently amended, Local Law 10 of 1981 and its amendment, Local Law 48 of 1991, dealt with elevator safety and inspections. According to Daniel DeBlasio, PE, an elevator consultant with the BOCA Group, an elevator/escalator consulting company based in New York City, new building codes went into effect on July 1, 2008 that have revamped the inspection and testing procedures for elevators and other “vertical transportation” equipment.
“Beginning in January of 2009, the old system of annual Local Law 10/81 inspections and two-year tests ended,” says DeBlasio. “They were replaced with a combined annual inspection and test for all elevators and escalators which must be performed (now known as a periodic inspection and Category One test) every year,” as well as a longer-range test that must be carried out every five years.
According to a recent article in the New York Times, New York has 54,806 passenger elevators and 3,985 freight elevators, all of which are subject to the new requirement. By the end of August 25, 2009, 777 inspections were completed, and violations were reported in 61 percent of the overall total number of inspections—a drastic increase from the 41 percent reported the previous year.
The new inspection/tests must now be performed by one company, and witnessed by another, DeBlasio continues. “Typically, the way it works is, the building’s usual maintenance contractor will perform the test, with a third-party private inspection agency hired by the owner to witness the test. The witnessing company cannot be affiliated with the maintenance contractor performing the test.”
According to DeBlasio, the five-year test requires a weight test procedure wherein weights equal to the total weight capacity for which the elevator is rated are placed in the cab, and the elevator is then run at full speed to each floor. The annual tests and the five-year tests also include testing under emergency power for buildings that have emergency generators. Inspection and test reporting must be signed by the performing inspector agency director (the maintenance contractor), the witnessing inspector (the witness technician), the agency director of witnessing inspector, and the elevator owner.
The requirement for independent licensed experts to witness an elevator inspection is at additional cost to the building. While Don Speranza, a partner with Brooklyn-based Nouveau Elevator was unable to provide The Cooperator with exact figures for witnessing, he says, “Witnessing from the third party is running anywhere from I would say $500 to $2,000—depending on how many times they have to go back and forth. This depends on if they are going to go back a second or a third time and how long the test is going to take. Sometimes you schedule a test and everyone is on board to do the first elevator, but then there’s another elevator shut down in that building so you can’t do the test. You can’t leave the building with no elevators, so they have to reschedule it. So what’s happening is that the owner is getting hit for the additional cost of those items.”
The inspector, as previously mentioned, is also licensed by the city, but typically works for the elevator owner’s maintenance provider.
Sense & Special Needs
While keeping up with inspections is crucial, nothing can take the place of good old common sense when it comes to assessing the elevator you’re about to step into.
Always be aware of any abnormal conditions that are going on with the operational functions of the elevator, says Speranza. “If there is something abnormal in the operation, call it into the management company or the elevator company directly. If a car isnot leveled, you should report that.”
If an elevator is ‘expressing’ without stopping on the correct floor that should be called in, he says, along with the doors not retracting or stopping properly when a passenger gets in. Also any shaking in the shaft or unusual noises should be reported. “Those are typical elevator concerns for general liability.”
Elevators also present particular usage and safety challenges to residents with special needs—particularly if the elevator was designed and installed before the passage of the Americans with Disabilities Act (ADA). The ADA set down guidelines for accessibility and usability standards for elevators, including everything from the reach range for button heights, to hands-free two-way communication, to the size of the cab in proportion to the door.
Even if your building hasn’t had to address the needs of a disabled resident yet, that doesn’t mean it couldn’t come up at any time. According to Douglas Boydston, president of Handi-Lift, a company based in Clifton, New Jersey that specializes in handicap-accessible elevators, “Even if a building doesn’t have any disabled tenants, there will still be visitors or relatives with special needs, or temporarily disabled people.”
If your building is undertaking a renovation of its lobby, you may be obligated to upgrade your property for ADA compliance, so it’s very important to research the issue before embarking on costly, time-consuming renovation plans. Certain co-ops are exempt from these regulations, and updating elevators to meet the ADA requirements is not usually mandated, but perhaps it’s time to consider doing so anyway for the safety and convenience of all your residents.
Staying on top of elevator maintenance should be a priority at all times, but it becomes even more important in buildings with disabled or elderly residents. Even minor malfunctions can cause serious problems for folks who, for whatever reason, might have difficulty negotiating stairwells or other uneven terrain.
“Leveling can be critical,” says Boydston. “If an elevator is not leveling properly, [stopping with the cab floor level with the building floor] even a half-inch low or high, that’s a serious hazard for someone who’s older or who uses a walker.”
Emergencies or malfunctions aside, Boydston says it’s important for administrators and their contractors to plan ahead for scheduled service interruptions and make proper accommodations for any disabled residents.
“It’s tough on [management] and on the residents when you have to shut down an elevator for two months,” he says. For residents who are unable to negotiate stairways, Boydston recommends installing a portable stair-climbing device such as the Stair-Trac. “The Housing Authority used the Stair-Trac when they were remodeling elevators in single-elevator buildings,” he says. “It can be an excellent solution for smaller buildings.”
Fix it, or Replace it?
In difficult economic climates, most boards are inclined to try and get as much mileage as possible out of their building equipment before shelling out for a big upgrade or total replacement. Even in more stable times, a co-op or condo board has a lot to ponder before embarking on an elevator project.
One of the first questions on deck is whether to hire a contractor directly, or spend some extra money for a professional elevator consultant. As with any other capital project, a co-op or condo can solicit bids from a number of elevator contractors, evaluate the bids, and choose a contractor to oversee the job. The decision-making process is more complicated than just going with the lowest bid, of course, but it need not present any more of a challenge for an experienced board than any other major capital undertaking.
Alternatively, a board might opt to bring in a consultant to handle the process for them. According to Martin Walsh, Jr. of Walsh Associates, Ltd. Elevator a Manhattan elevator consulting firm, “Consultants represent the owners’ interest in the project. We design the elevator system for them, put the project out to bid, manage the bidding process, select vendors in conjunction with the owners, and manage the project as it progresses. Owners and co-op boards have no way of guaranteeing apple-to-apple pricing, and they may lack the technical competency to evaluate bids.”
Regardless of whether a building hires a consultant or goes it alone, final costs and time frames for elevator work vary considerably, depending on the size and scale of what needs to be done.
In any case, an elevator project isn’t an overnight job, and it’s almost never cheap. According to Speranza, “You want to spend your money wisely, you want to make sure there’s a time and a place for everything. So, if the elevator is breaking down and you can afford the shutdowns and long lead time to get the elevators back up and running, then you can choose to do a modernization.”
And modernizations, he explains, are long-term capital items that a building will do once every twenty-plus years. The project depends on building size, capacity, and speed of the elevator. “Ballpark,” he adds, “you can go from $100,000 to $500,000.”
Warranties on parts and service can range from no warranty at all to five-, ten-, or 20-year, full-service contracts. Most parts come with a one-year warranty. On maintenance contracts, Hayes warns against signing any contract other than a full-service contract, which “spells out everything that the contractor needs to repair and replace.” If a specific part is not mentioned in the contract, it may not be covered, so he advises building administrators to make sure that the parts are named individually.
Other Considerations
As with bodily health, so too with elevator health: An ounce of prevention is worth a pound of cure.
According to Speranza, mechanics use a preventative maintenance log book as a guideline to performing monthly maintenance procedures. The amount of time needed for such maintenance varies and depends on usage and demand, the height of the elevators, how big they are, and how fast they travel.
“A six-story building would need say two to four hours of monthly maintenance, whereas other elevators for buildings 20-stories high or above would need anywhere from six to eight hours per month. It all depends on the formula of ingredients for each building and with that there’s a guideline for doing things monthly, quarterly or yearly,” says Speranza.
Therefore, whether renovating an existing elevator, installing a new one, or just plugging along with what they’ve got, co-ops and condos should insist on regular inspections, design features that promote safety, and safe, conscientious use by all building residents and visitors.
Hannah Fons is the associate editor of The Cooperator.
9 Comments
Leave a Comment